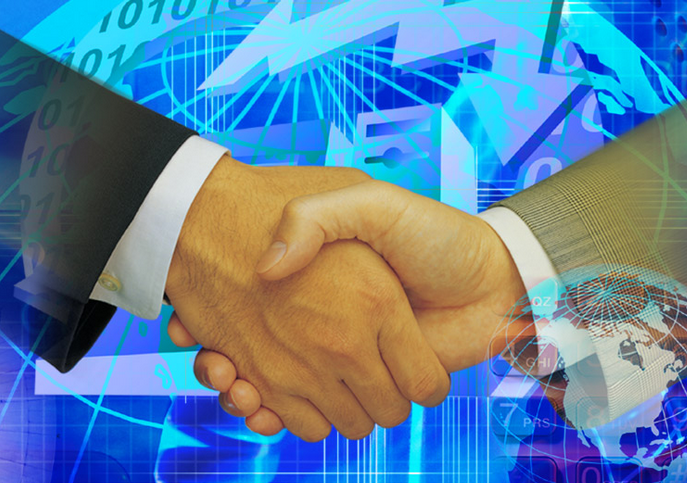
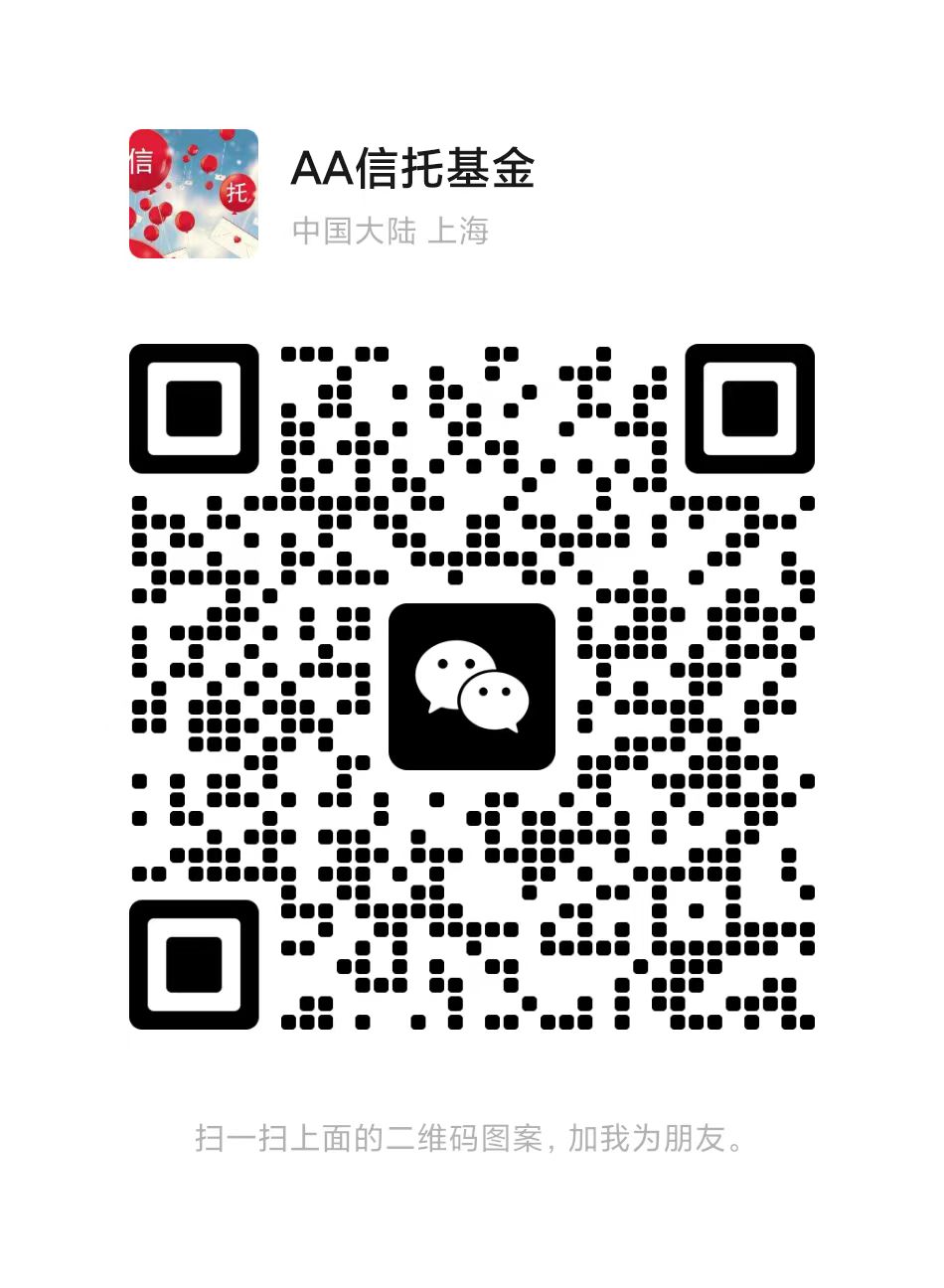
添加微信好友, 获取更多信息
复制微信号
无关内容:
粉喷桩,挤密碎石桩,塑料排水板打入深度,间距达不到设计要求②,粉喷桩复搅深度达不到要求或喷粉量未达到设计要求,③,挤密碎石桩未进行反插
④,预压或超载预压沉降未稳定,即卸载
⑤,软基处理质量未达到设计要求
⑥,桩未打入软弱层
防治措施:①,粉喷桩,挤密碎石桩,塑料排水板打入深度,间距应达到设计要求
②,粉喷桩复搅深度达不到要求或喷粉量应达到设计要求,③,挤密碎石桩应进行反插,④,应进行连续的沉降观测,待沉降稳定后方可卸载
⑤,在现场进行试桩,按试桩结果调整设计桩长
1.2:路基出现纵向裂缝和错台 形成原因:①
清表不到位,路基底存在软弱层
②,沟塘清淤不彻底,清淤回填不均匀或压实度不足
③,路基压实度不均匀
防治措施:①,应认真清表及时发现路基底暗沟,暗塘
②,沟塘清淤应清理干净,并采用水稳定性好的材料严格分层回填,并达到设计压实度
③,提高路基压实度
1.3:路基出现滑裂面 形成原因:①,基底存在软土且厚度不均匀
②,淤泥清除换填不彻底
③,填土速率过快
防治措施:①,软土处理要到位,并及时发现暗沟暗塘
②,加强沉降和侧向位移观测,及时发现侧滑苗头
2路基 2.1:路基碾压出现“弹簧” 形成原因:①,碾压时土的含水量超过最佳含水量
②,高塑性粘性土“砂化”未达到应有的效果
③,翻晒,拌和不均匀
④,碾压层下存在软弱层
防治措施:①,低塑性高含水量的土应翻晒到规定含水量方可碾压
②,高塑性粘性土难以粉碎,应进行两次拌灰并存放一段时间,使其充分“砂化”
③,对产生“弹簧”的部位翻挖掺灰后从新碾压
2.2:路基压实度不够 形成原因:①,碾压遍数不够
②,压路机质量偏小
③,松铺厚度过大
④,碾压不均匀,局部漏压
⑤,含水量偏离最佳含水量超过规定值
防治措施:①,确保压路机的质量及碾压遍数符合规定
②,采用振动压路机配合三轮压路机碾压保证碾压均匀
③,压路机应进退有序,前后应有重叠
④,路基土应在接近最佳含水量时进行碾压
2.3:路基积水严重 形成原因:①,路基表面不平整
②,路基表面未设横坡或出现倒坡
防治措施:①,路基压实前应整平
②,路基表面应设2%~4%的横坡
2.4:路基边坡被冲刷 形成原因:①,过早的削坡而边坡防护工程未能及时跟上
②,未设临时急流槽和拦水埂
③,每次雨水冲刷后未及时修补路基
④,边坡未植草防护
防治措施:①,削坡后边坡防护工程应及时跟上
②,应设临时急流槽和拦水埂和排水沟
③,应及时填补冲沟
2.5:压实层表面松散 形成原因:①,施工路段偏长,拌和,粉碎,压实机具不足
②,粉碎,拌和后未及时碾压表层失水过多
③,压实层的土含水量低于最佳含水量过多
防治措施:①,确保压实层土的含水量与最佳含水量差在规定范围内
②,适当洒水后重新进行拌和碾压
2.6:路基表面网状裂缝 形成原因:①,土的塑性指数偏高或为膨胀土
②,碾压时含水量偏大,且未有及时覆土
③,压实后养护不到位,表面失水过多
防治措施:①,采取合格的填料,或采取掺灰处理
②,选用符合规范要求的土料填筑路基,确保压实层土的含水量接近最佳含水量
③,加强养护,避免表面水分过多损失
④,认真进行施工组织安排
2.7:路基表面起皮 形成原因:①,压实层土的含水量不均匀且失水过多
②,为调整高程而贴补薄层
③,碾压机具不足,碾压不及时,未配置胶轮压路机
防治措施:①,确保压实层土的含水量均匀且与最佳含水量差在规定范围内
②,认真进行施工组织计划,配备足够合适的机具保证翻晒均匀,碾压及时
2.8:路基表面出现放炮 形成原因:石灰消解不充分
防治措施:石灰应在使用前7~10天进行充分消解,并过10㎜筛
2.9:路基压实度超密 形成原因:①,未认真进行标准击实试验,最大干密度误差较大
②,路基填料不均匀
③,采用重型压实机械,压实功偏大
防治措施:①,在取土坑取具有代表性的土样认真进行标准击实试验,不同土样硬分别进行标准击实试验
②,选择均匀的填料
2.10:路基灰土灰剂量不均 形成原因:①,路基土的砂化不充分
②,路基掺灰未按工艺要求划格洒灰
③,拌和不均匀
防治措施:①,液限较大粘性土应充分砂化
②,应严格按掺灰路基施工工艺要求进行划格洒灰,粉碎拌和,采用稳定土拌和机进行拌和
2.11:路基灰土灰剂量不足 形成原因:①,施工单位偷工减料,未按规定打格撒灰
②,石灰堆放时间过长;或拌和碾压不及时
③,较长时间堆放的石灰未覆盖
防治措施:①,确保石灰掺量
②,石灰消解后要在7~10内及时用完
③,堆放时间较长的石灰,应事先用彩条布或土覆盖,使用前重新测定钙镁含量,必要时重新调整掺灰剂量
④,撒灰后应及时拌和碾压
2.12:路基边缘压实度不够 形成原因:①,压实机具未走到边缘
②,路基填筑宽度不足,未实行超宽填筑
防治措施:①,路基按设计要求超宽填筑
②,控制碾压工艺,压路机一定要行使到路基边缘
3路面工程 3.1:路面底基层 3.1.1:二灰土抗压强度不合格 形成原因:①,石灰剂量不足,石灰等级较低,粘土粉碎不够,拌和不均匀
②,二灰土抗压试件制备不标准,高度超标,密度较小
③,试件养护温度湿度不符合要求,养护时间失水过多 防治措施:①,实际石灰剂量应比设计剂量高出0.5~1.0个百分点
②,采用有效钙加氧化镁含量较高的石灰,并充分消解
③,土块粉碎至规定尺寸,拌和均匀
④,二灰土试件高度误差应在±0.2㎜范围内
⑤,试件应有塑料膜裹覆养生,养生温度湿度应在规定范围内
3.1.2:二灰底基层表面起皮 形成原因:①,二灰土含水量过大或过小
②,二灰土表面失水过多,未及时碾压
③,碾压未按先轻后重的原则
④,二灰土拌和不均匀
防治措施:①,二灰土的含水量宜大于最佳含水量1%开始碾压
并及时压实②,及时消除粘附在压路机轮上的二灰土
并清除路面以外
③,应按先轻后重的碾压程序逐步压实
④,对表面起皮层应清除路面以外,标高用基层补足,也可及时刨松厚度不小于10㎝打碎洒水拌匀后压实
⑤,严格按放样线施工,不得采用贴补薄层的方法不足高程
3.1.3:失去粘结力 形成原因:①,沥青混合料中石料与沥青的粘结性差
②,石料含泥量高,石料表面被泥浆裹覆
③,沥青路面空隙率过大,导致沥青砼长期受水浸害
④,沥青用量不足
⑤,石料被压碎或石料吸水性大
⑥沥青拌和过程中温度偏高,产生老化
防治措施:①,掺加抗剥落剂
②,严格控制石料含泥量
③,完善沥青混合为配合比,调整压路机具组合,控制压实度
④,按施工配合比控制沥青用量
⑤,严格控制沥青混合料拌和温度
4桥梁工程 4.1混凝土浇筑 4.1.1:混凝土强度较低 形成原因:1,无堆放水泥的库房,水泥堆放在未进行硬化的地面;水泥库房的地面没有硬化或防潮措施,至使水泥受潮,水泥标号降低,影响砼强度
2,不同规格的石料混堆
碎石的压碎值`真片状`级配等指标达不到要求,砂石料的含泥量过大,黄沙中含有较多的木炭,卵石`泥块等杂质,黄沙的级配差,石英含量低
3,砂石料和拌和用水计量不准或根本就没有计量
4,混凝土拌和用水不符合要求
5,未按审批的配比进行施工
防治措施:1,应选择在地势较高处搭设地面硬化`且有防潮处理的水泥库房
2,对进场用砂石料进行自检优选,选用含泥量低的砂,扩大砂石料的堆放场地,并进行硬化,分类堆放
应用高压水泵对含泥量高的粗集料进行冲洗
3,现场应设置计量设备,砼浇筑前应测定砂石料含水量
4,应选择合格的拌和及养生用水
5,严格按审批的砼配比进行施工
4,1,2:混凝土构件出现裂纹,裂缝 形成原因:1,水泥安定性不合格
2,大体积砼未采用缓凝和降低水泥水化热的措施
3,未及时养生
4,同一结构物的不同位置温差大,导致砼凝固时因收缩所产生的收缩应力超过砼极限抗拉强度或内外温差较大表面抗拉应力超过砼极限强度而产生裂缝
5,基础与支架的强度`刚度,稳定性不够引起裂缝
防止措施:1,采用安定性合格的水泥
2,大体积砼应优选矿渣水泥,粉煤灰水泥等低水化热水泥
3,优化配合比:改善骨料级配,降低水灰比,掺加粉煤灰等混合材料,掺加缓凝剂
4,采用遮阳篷的降温措施以降低水化热,推迟水化热峰值出现
5,及时养生
6,同一结构物的不同位置温差应在设计允许范围之内
7,基础与支架应有较好的强度,刚度,稳定性并应采取预压措施
4,1,3;混凝土构件出现冷缝 形成原因:大构件砼分层浇筑时,砼浇筑间断时间较长,下一层浇筑的砼已经初凝才浇筑上一层,将导致浇筑的砼形成低强度的夹层
防止措施;1,大构件砼分层浇筑时间较长,应增加搅拌能力
2,掺入缓凝型减水剂
3,改善浇筑工艺确保分层浇筑的间断时间小于前层砼的初凝时间
4,1,4:混凝土离析 形成原因:1,集料级配不合格引起离析
2,砼自由倾落高度大而未设置减速装置
3,浇筑过程中过振
防止措施:1,采用级配合格的集料
2,砼自由倾落高度超过2米时,应设置串筒,溜槽,或振动溜槽等设施,且串筒出料口下面的砼堆积高度不得超过1米,倾落高度超过2米时,应设置减速装置
3,振捣时,砼停止下沉,不再冒出气泡,表面呈现平坦,泛浆即可,不得超振
4,1,5:混凝土表面有蜂窝,麻面,气孔 形成原因:1,砼浇筑时漏振
2,模板漏浆
防止措施:1,砼浇筑过程中插入式振动器的移动间距不应超过其作用半径的1.5倍,与侧模应保持5~10㎝的间距,插入下层砼5~10㎝的深度
2,表面振动器移位应能覆盖已振实部分
3,控制砼分层浇筑厚度,对于插入式及附着式振动器不宜超过300㎜
4,模板拼接紧密,并加止水带,防止漏浆
4,1,6:混凝土施工出了质量差 形成原因:1,施工缝未凿毛
2,用钢筋拉毛代替凿毛
3,施工缝凿毛过早导致砼表面松散
防止措施:1,应在设施工缝的先浇砼强度达到2.5MPa后进行凿毛
2,凿毛后毛面应用清水洗刷干净
4,1,7:混凝土漏浆,表面平整度差 形成原因:1,模板周转次数较多表面不平整
2,模板刚度不够而造成变形
3,相邻模板拼缝过宽且未做有效处理
4,模板的榫槽嵌接不紧造成跑模
防止措施:1,采用平整度好,刚度符合要求的模板
2,处理好模板拼缝
3,将模板的榫槽嵌接紧密
4,1,8;砼构件表有泌水现象,色差大 形成原因:1,砂石料极配差
2,矿渣水泥泌水性较大,导致砼表水性差
3,振捣过度
防止措施:1,应确保砂石料具有良好的级配
2,采用泌水率小的水泥
3,振捣恰当
4,2: 钢筋制作与安装 4,2,1:钢筋接头设置不符合要求 形成原因:无专门技术人员配筋或配筋人员技术水平较低,对接头所形成的弱强度断面的危害性意思不够
防止措施:1,应专门技术人员配筋,同时提高配筋人员业务水平
2,受拉主钢筋焊接接头应避开最大应力断面
3,受拉主筋接头在同一断面数量不得超过50%
4,钢筋接头距弯起点距离应不小于10d 4,2,2:预制安装的钢筋骨架扭曲 形成原因:1,未在坚固的工作平台上进行安装
2,钢筋骨架刚度,稳定性不够时未增设加强钢筋
防止措施:1,应在坚固的工作平台上进行钢筋骨架的拼装焊接
2,钢筋骨架刚度,稳定性不够时应增设加强钢筋
4,2,3:焊接钢筋不处在同一轴线上 形成原因:1,搭接焊的钢筋接头未打折
2,搭接焊的钢筋接头先焊好后再打折成S形
3,闪光对焊的接头有错位
4,帮条焊只有一根帮条
防止措施:1,搭接焊的钢筋接头焊前应先打折
2,闪光对焊的接头应对齐
3帮条焊应有两根帮条
4,2,4:焊接强度不够 形成原因:1,电流过大,钢筋接头局部烧伤
2,搭接焊,帮条焊焊缝长度宽度不足,焊渣未及时清除
3,未能选择合适的焊条,4,冬季焊接过火
5,焊接后接头骤冷
防止措施:1,选择合适的焊条,并且使用前在烘箱烘干
2,冬季焊接防过火
3,焊接后接头防骤冷
4,应进行岗位培训,持证上岗
4,2,5:钢筋受污染,锈蚀严重 形成原因:1,钢筋加工场地没有硬化
2,安装好的钢筋没有用垫块垫好
3,没有采取防雨防潮措施
4,钢筋加工安装后长时间不浇筑
防止措施:1,钢筋加工场地应硬化
2,安装好的钢筋用垫块垫好
3,采取防雨防潮措施
4,钢筋加工安装后要及时浇筑
已锈蚀的钢筋要用钢丝刷除去浮锈后方可浇筑砼
4,2,,6:钢筋间距不一,钢筋保护层厚度不足,盘圆钢筋使用前不调直 形成原因:1,质量意思差,责任心差
2,质保体系不健全,没有认真进行自检
3,保护层垫块偏小或偏薄
防止措施:1,提高施工人员质量意思,加强工作责任心,认真进行自检
2,安装足够的合格的保护层垫块
3,盘圆钢筋使用前调直
4,3:钻孔灌注桩 4,3,1:钻孔灌注桩断桩 形成原因:1,集料级配差,砼和易性差而造成的离析卡管
2,泥浆指标未达到要求,钻机基础不平稳,钻架摆幅过大,钻杆上边没有导向设备,基底土质差甚至出现流沙层而至使扩孔或塌孔而引起的浇筑时间过长
3,搅拌设备故障而无备用设备引起砼浇筑时间过长
4,砼浇筑时间超过砼初凝时间
5,砼浇筑过程中导管埋置深度偏小,则管内压力过小
6,导管埋深过大,管口的砼已凝固
防止措施:1,确保良好的集料级配差和砼和易性
2,应坚持清孔确保泥浆的粘度,比重,砂率指标达到要求
3,钻孔前钻机平台应进行超平
4钻机平台基础应垫实
5,钻杆上边应有导向设备
6,对于有流沙层的桩基掺加膨润土,纤维素
铬铁木质素磺酸钠盐,煤碱剂,碳酸钠等比重低,粘度好固壁能力强的外加剂以加强泥浆的粘结性能
7,搅拌设备工作状态应良好,并配有备用设备
8,确保导管的埋深控制在2~6米范围内
9,混凝土灌注期间,间歇时间不应大于混凝土初凝时间
10,导管下口至孔底的距离本应过大,以保证导管的初始埋深
4,3,2:桩身混凝土强度偏低 形成原因:1,未按设计配合比进行施工
2,导管下口初始埋深过小引起夹泥
3,清孔不到位置而引起夹泥
防止措施:1,严格按设计配合比进行施工
2,导管下口初始埋深不应小于1米
3,应彻底清孔
4,3,3:桩头主筋偏位大,将桩头钢筋扳成折线状态进行调整 形成原因:1,施工人员责任心不强,施工控制不到位
2,施工放样不准确
防止措施:1,增强施工人员责任心,加强施工管理,确保放样精度
2,桩头主筋偏位大时应往下破除直到桩基钢筋倾斜度调至允许值以内
4,4:梁,板制作与安装 4,4,1:梁,板体裂缝 形成原因:1,预制梁底模或支架基础不密实或强度较低,引起不均匀沉降导致梁体裂缝
现浇箱梁支架不均匀沉降引起梁体开裂
2,用标准养护的砼试块强度作为施加张拉的条件,当标准养护的砼试块强度达到设计的张力强度时,由于梁板养护条件不同于标准养护,其强度可能尚未达到设计的张力强度,如果进行张力,易导致大梁负弯距区产生裂缝
3,砼石子的最大粒径过小,级配差使砼的弹性模量偏小
4,波纹管道于梁宽方向的偏位造成梁端负弯距偏心而引起的预应力梁端部侧面有纵向裂缝
5,波纹管竖向偏位过大,造成零弯距偏位
6,冬季施工时,蒸汽养护升温或降温速度过快,易引起大梁的温差裂缝
7堆放时支点位置不当造成大梁处于受扭状态产生裂缝甚至剪断
8,梁板出坑起吊不规范,与底模表面吸力过大而裂缝
防止措施:1,应对底模或支架基础进行预压,加强基础的强度,刚度和稳定性,坚持现浇箱梁支架按设计要求预压和沉降测量,并应保留完整记录
2,砼石子的最大粒径不宜过小
3,保证砼有较好的级配
4,坚持砼的弹性模量试验,5,应将控制张拉的抗压强度试块与梁同条件养护,待强度达到规定值方可张拉
6,波纹管位置应符合设计要求
7,钢绞线张拉顺序应符合设计规定
8,蒸汽养护应准备测温装置,控制降温在5ºC~10ºC/h,做好升温,恒温和降温记录
9,堆放时支点位置应对称,斜撑应设在翼板跟部,不能撑于翼板外缘
10,梁板出坑应从一头轻吊,消除底模表面间的真空后再双吊
4,4,2:预应力损失过大 形成原因:1,未及时进行孔道压浆而导致钢绞线锈蚀
2,压浆不饱满或水泥浆强度低引起握裹力不够
3,在孔道水泥浆强度未达到梁板自身砼强度的60%也未超过22MPa时即进行吊运,导致水泥浆开裂,握裹力降低
4,压浆后未及时封锚导致锚端锈蚀
5,用电弧焊或氧焊割断已张拉的钢绞线
防止措施:1,应在张拉后14d内进行孔道的水泥压浆,并应保留孔道压浆记录
做好水泥压浆的抗压试块
2,在孔道水泥压浆强度达到梁板自身强度的60%且大于22MPa时才能进行吊运
3,压浆后应及时封锚
4,用砂轮等冷切割方式割断钢绞线
4,4,3:梁的起拱值偏或偏小 形成原因:波纹管竖向偏位过大,造成零弯距轴偏位,则最大正弯距发生变化较大导致梁的起拱值过大或过小
2,用标准养护的砼试块弹性模量作为施加张拉的条件,当标准养护的试块强度达到设计的张拉强度时,由于梁板养护条件不同,其弹性模量可能尚未达到设计值,导致梁的起拱值大
3,砼弹性模量不稳定导致梁的起拱值的不稳定
4,钢绞线的自检频率不够,钢绞线张拉双控的伸长值指标计算时弹性模量值均采用2*105MPa或采用其他批的钢绞线的弹性模量值
当计算所采用的钢绞线的弹性模量值大于实际钢绞线的弹性模量时,则计算伸长值偏小,这样造成了实际预应力不够
当计算所采用的钢绞线的弹性模量值小于实际钢绞线的弹性模量时,则计算伸长值偏大,这样造成超张拉
实际预应力超过设计预应力易引起大梁的起拱值大,且出现裂缝
5,未推算初应力伸长值,而是在施加应力之前设置一个零点致初应力时的位移作为初应力伸长值,不符合规范规定
则导致钢绞线实际伸长值小于要求伸长值,造成了实际预应力不够,拱值小于设计值
6,持荷时间不足
防止措施:1波纹管的安装要准确
2,控制张拉的试件应与梁板条条件养护
3,增加钢绞线的自检频率
伸长值的计算采用同批钢绞线弹性模量的实测值
4,张拉时应将钢绞线10%~20%σK之间的测量伸长值作为初应力10%的伸长值,一般待张拉倒10%σK时相对于一基准点量一长度,再等到20%σK时相对于该基准点量一长度,两长度之差△L2即为初应力时的推算伸长值
5,应按要求的时间持荷
4,4,4:梁体混凝土出现空洞 形成原因:1,钢筋较密砼振捣不实
2,配合比设计不合理
3,因锚板为倒坡倾向梁端,其后面砼不宜浇筑,由于振捣不够,砼出现空洞
防止措施:1,调整混凝土配合比,如减小集料粒径,增加砼混合料坍落度,掺入碱水剂
2,应采用小直径的振捣棒加强振捣,改进浇筑工艺
4,4,5:现浇连续箱梁横断面方向所设置的施工缝有错台 形成原因:1,测量放样不准确
2,模板未与先浇砼面衔接好
3,基础预压未稳定
防止措施:1,准确测量放样
2,做好模板与先浇砼面衔接好3,基础预压稳定后方可进行浇筑
4,4,6:板梁铰接缝未按规范进行凿毛 形成原因:施工单位质量意识差,对板梁铰接缝凿毛的重要性认识不足
防止措施:应对板梁铰接缝凿毛引起足够的重视,待板梁砼达到一定强度后进行凿毛,以确保铰接缝连接质量符合要求
4,4,7:板梁支座脱空 形成原因:1,支座高程未控制好
2,支座垫石顶的砂浆还未干,即放好支座安装梁
3,预制板梁底板翘曲
防止措施:1板梁安装前应做好测量工作;调整支座到规定高程
2,应待支座垫石顶的砂浆稍凝固再安放板梁
3,预制板梁底板应平整,无翅曲
4,4,8:板梁支座偏位较大 形成原因:1,放样不准确
2,施工控制不到位
防止措施:1,做到准确放样
2,采用不同的基准线校核
4,4,9:支座垫块不平整 形成原因:质量意识差 防止措施:1,采用水平尺检查
2,应用砂浆整平或用钢板垫平
4,4,10:安装好的梁底未勾缝 形成原因:河道上不易搭支架
防止措施:1,应于桥面上安装挂蓝脚手架进行勾缝
2,于桥下搭设脚手架勾缝
4,4,11:桥梁伸缩缝损坏 形成原因:浇筑砼强度低
2,砼未及时养护
3,伸缩缝安装不合格
防止措施:1,确保砼强度合格
2,砼应及时养护
3,根据施工气温和设计要求设置安装时的缝宽,接缝钢筋与梁,台钢筋焊接顺序应符合设计规定
4,5:桥头跳车 形成原因:1,压实机具不适用,使得靠近台背处回填土压实不够,工后沉降大
2,软基路段台前预压长度不足
3,软基路段桥头堆载预压卸载过早
4,软基路段桥头处软基处理深度不到位,质量不符合设计要求
5,回填厚度过大以及回填不及时积水而引起的桥头回填土压实度不够
防止措施:选择合适的压实机具,确保台背回填压实度达到要求
2,保证足够的台前预压长度
3,连续进行沉降观测,保证桥头沉降速率达到规定范围后再卸载
4,确保桥头软基处理深度符合要求,严格控制软基处理质量
5,在台背画回填层厚线,确保回填厚度在规定范围内
6,及时回填
5通道及涵洞 5,1:结构构件裂缝,裂纹 形成原因:1,水泥安定性不合格
2,没有及时养护
防止措施: 1,做好砼配合比
2,加强早期养护
3,对水泥的技术性质加大频率检验
5,2:结构物表面出现冷缝 形成原因:下一层浇筑的砼已凝固再浇筑上一层的砼
防止措施:1,应加强搅拌能力
2,改善浇筑工艺以确保混凝土浇筑间断时间小于前层砼的初凝时间
5,3:施工缝表面砼松散 形成原因:凿毛过早 防止措施:应在砼强度达到2.5MPa以上时方可凿毛
5,4:施工缝表面蜂窝,麻面 形成原因:集料级配差
2,砼浇筑时漏振
防止措施:1,确保良好的集料级配
2,砼浇筑过程中插入式振动器的移动间距不应超过其作用半径的1.5倍,与侧模应保持5~10㎝的距离,插入下层砼5~10㎝的深度
3,表面振动器移位应能覆盖已振实部分
4,控制砼分层浇筑厚度,对于采用插入式及附着振动器施工不宜超过300㎜
5,5混凝土表面不平整 形成原因:1,模板周转次数较多表面不平整
2,模板刚度不够而造成变形
防止措施:1,采用平整度好,刚度符合要求的模板
5,6:拉条螺丝处外观较差 形成原因:处理方法不当
防止措施:应先凿除钢筋周围直径4~5㎝,深2~3㎝的水泥砼后割除钢筋,再修补
北起五亭路,南止振兴东路,是兴化市今年实施新城建造的主要工程之一
道路设计红线宽30米,一块板型式,快车道宽15米,两侧人行道各为4.1米,该段工程量如下: 1.φ60管道400米; 2.φ23管道75米; 3.人孔50座; 4.雨水井50座; 5.路牙1600米; 6.砼路面6000平方米; 7.人行道3280平方米; (二)工程执行定额及编制依据 1.兴化市新区道路建设工程招标文件
2.1991年《江苏省市政工程单位估价表》
3.全国统一施工机械台班费用定额(1999年江苏地区预算价格)
4.1996年6月版《江苏省市政、房屋修缮、仿古建筑及园林工程费用定额》
5.兴化市2001年第三期建筑材料指导价
6.取费标准:道路及下水道均采用16.65%间接费率,计划利润率3.5%
7.兴化市规划设计院施工设计图
工作文件夹.rar 4d22dc51cc0baab3d8e473c8f658322a.rar (26.39 KB)
A类央企信托-非标淮安政信